Gli impianti industriali sono sempre più orientati alla massimizzazione della continuità del processo produttivo, che viene ottenuta anche con la crescente automazione. Come conseguenza assistiamo ad una sempre più massiccia presenza di apparecchiature elettroniche/informatiche nelle linee produttive.
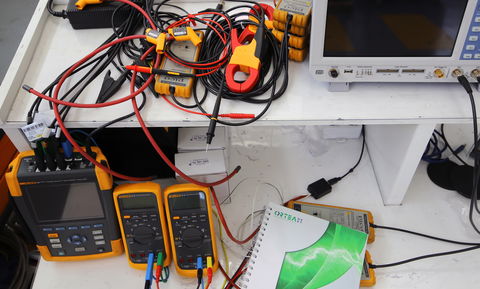
Per poter garantire elevate performance produttive, gli impianti industriali devono quindi essere alimentati con energia elettrica di ottima qualità, sia in termini di continuità che di caratteristiche intrinseche. Le problematiche di cattiva qualità dell’energia elettrica sono infatti una delle principali cause di fermo impianto non programmato, di malfunzionamenti, di danni alle apparecchiature ed alle infrastrutture elettriche.
Da questo punto di vista bisogna sottolineare che, secondo studi statistici, circa l'80% dei disturbi di cattivo power quality è generato internamente all’impianto dell’utente finale ("da valle"), tipicamente da carichi non lineari come inverter, saldatrici/puntatrici, azionamenti, robot, apparecchiature elettroniche che generano la presenza delle armoniche sulla rete, o per la presenza di carichi con grande potenza (grossi motori, ad esempio) che possono generare delle perturbazioni tipicamente in fase di avviamento o di arresto.
Il restante 20% dei disturbi proviene dalla Rete ("da monte"), ovvero dal fornitore di energia, poiché anche i sistemi di trasmissione e distribuzione più avanzati non sono in grado di garantire la fornitura con assoluta continuità e con perfetta qualità; in tal senso la recente complessità del mondo della generazione (pensiamo alle FER, ed alla loro crescente diffusione) ha sicuramente avuto un impatto non indifferente sulla qualità della tensione fornita.
Affrontare una problematica di Power Quality non è quasi mai una faccenda semplice. Innanzitutto bisogna capire se il problema arriva “da monte” o “da valle”, e poi capire dove, quando e come si manifesta… Per raccogliere informazioni e dati elettrici sui quali ragionare è necessario effettuare una o più misurazioni, se non vere e proprie campagne di misura. Bisogna avere competenze misuristiche, impiantistiche, di prodotto, e di processo; nonché avere chiaro cosa accade. Difficilmente una sola persona domina tutti questi ambiti in modo tale da poter affrontare un determinato problema, in un determinato impianto: bisogna affrontarlo in team! Coinvolgendo più figure ovvero l’esperto di misure elettriche (che spesso è anche esperto di impianti), l’esperto di soluzioni (solitamente uno specialista di soluzioni di PQ), e per quanto riguarda la comprensione del processo e del problema in corso, inevitabilmente bisogna coinvolgere il personale del cliente (responsabile di produzione e/o responsabile impianto elettrico): nessuno meglio di loro può avere le informazioni su ciò che accade, anche se spesso è noto l’effetto e non la causa che lo ha generato.
Qui nel seguito faremo solo qualche cenno all’importanza delle misure; questa tematica è ampia, e merita delle riflessioni, perché rappresenta un punto fondamentale per poter risolvere un problema di PQ: è il primo passo nel processo di indagine, e se viene fatto nella direzione sbagliata porterà inesorabilmente ad un fallimento.
Innanzitutto bisogna dialogare in modo esaustivo con chi conosce bene il processo e i problemi riscontrati: cosa accade, in quali situazioni di impianto accade, in quali ore, in quali giorni, in quale stagione. Se i problemi sono iniziati dopo o prima di eventuali modifiche all’impianto (ad esempio, aggiunta di fotovoltaico, incremento di linee produttive ecc). Se le problematiche coinvolgono un determinato macchinario, sarebbe bene dialogare anche con il relativo costruttore per capire il motivo di determinati comportamenti non corretti.
Ricadono all’interno di questa fase anche le verifiche documentali; in primis la lettura dello schema verificando che corrisponda al vero e che non sia eccessivamente obsoleto: questo documento è fondamentale per poter individuare utenze distorcenti ed utenze sensibili, capire quali sono le utenze coinvolte da malfunzionamento. Anche la lettura delle bollette di un intero anno solare è importante, specialmente in caso di impianti che non hanno un funzionamento continuativo.
Ove ci fosse un sistema di supervisione con registrazione di dati, va sicuramente consultato, verificando che gli strumenti di misura in campo forniscano dati veritieri.
Se possibile, prima delle misure si può fare un sopraluogo per esaminare l’impianto: si possono raccogliere informazioni importanti, anche su base “sensoriale” ovvero con la vista (stato dei macchinari, evidenze di corto circuito, surriscaldamenti, corrosione, presenza di inquinamento da polveri magari conduttive, etc), con l’udito (ronzii in cabina, e loro andamento in funzione dei carichi attivi), o “a pelle” (temperatura in cabina, umidità).
Una volta inquadrata la situazione, si deve riflettere e decidere come condurre l'attività di misura, ovvero dove/quando/per quanto tempo/quali misure fare. La scelta è strategica, fondamentale, poiché le misure devono fornire gli elementi sui quali ragionare e risolvere il problema. Ma non devono essere fatte misure a sproposito, viceversa il problema si complica, e la mole di dati da analizzare e gestire può diventare inutilmente imbarazzante. Come pure non ha senso avere tutti i risultati di una campagna di misura, anche ben condotta, senza sapere nulla dell’impianto di cui si parla, in quali punti dell’impianto sono state effettuate le misure, quando, in quali condizioni produttive. Purtroppo, spesso chi esegue le misure si preoccupa solo di inviare il file con i risultati, e nient’altro… nessuna informazione “al contorno”.
E’ fondamentale in una campagna di misure determinare:
Dove: in quali punti dell’impianto eseguire le misure. Ai morsetti dei carichi disturbati, ai morsetti dei carichi disturbanti, appena a valle del trafo MT/bt... In impianti con topologia complessa la scelta del punto in cui misurare è fondamentale: sbagliare il punto di misura significa poi dover “buttare” tutte le misure fatte e dover ripartire da capo.
Quando: in corrispondenza del pieno carico dell’impianto (o dell’avviamento dei principali carichi) se si vuole misurare la massima distorsione armonica di corrente e tensione, e/o la minima tensione. Oppure, se si vogliono valutare eventuali variazioni della tensione al di sopra del valore nominale: misurare in corrispondenza delle ore vuote di fascia F3 e/o con impianto al minimo. In caso di problematiche riscontrate in occasione di determinate lavorazioni o stati dell’impianto, va da sé che le misure devono essere condotte riproducendo il più possibile queste condizioni. Attenzione agli impianti con funzionamento “stagionale”, quali ad esempio il trattamento di frutta/verdura, oppure impianti con annesso fotovoltaico in scambio: le misure devono essere fatte nella stagione giusta, viceversa sono inutilizzabili.
Per quanto tempo: le misure orientate ad individuare max THDI e max THDV possono davvero durare anche pochi quarti d’ora, purchè, come accennato sopra, eseguite quando davvero l’impianto è al massimo carico. Le misure orientate alla profilazione della tensione o delle potenze invece vanno condotte almeno per una settimana completa (CEI EN 50160 docet). Indagini su basi statistiche (ad esempio il conteggio dei buchi di tensione e relative caratteristiche di durata e profondità) hanno bisogno di una misurazione continuativa di almeno qualche mese. Meglio ancora riferirsi alle informazioni disponibili dal distributore dell’energia, che fornisce i buchi di tutto l’anno solare precedente, registrati alle semisbarre della cabina primaria di riferimento: anche se sono informazioni un po' "vecchie", forniscono una base statistica fondamentale.
Quali misure fare, quali strumenti utilizzare: dipende da tanti fattori, non è possibile generalizzare. Bisogna valutare caso per caso, e qui sta l’abilità ed il valore aggiunto degli esperti di misure elettriche.
Ortea propone servizi di misura del Power Quality in impianti di potenza, sia industriali che del terziario, orientate all’individuazione di problematiche di distorsione di tensione/corrente, variazioni di tensione lente/rapide. Con individuazione e proposta tecnico-commerciale di soluzioni di rifasamento/filtraggio/stabilizzazione.